Los engranajes cónicos son un tipo de engranaje caracterizado por tener dientes dispuestos sobre una superficie cónica, lo que permite transmitir movimiento entre ejes que se cruzan, generalmente en ángulo recto. Este diseño los diferencia claramente de los engranajes cilíndricos, que trabajan únicamente entre ejes paralelos, y les otorga una versatilidad única en diversas aplicaciones industriales y automotrices.
Su geometría específica permite transferir potencia de forma eficiente entre ejes no paralelos, lo que los convierte en piezas fundamentales en transmisiones angulares, especialmente cuando se busca un equilibrio entre precisión, rendimiento mecánico y durabilidad.
Geometría y funcionamiento
En su forma más básica, un engranaje cónico está compuesto por dos ruedas dentadas con forma de tronco de cono, cuyos dientes están tallados de manera que coincidan en la intersección de sus ejes. A este punto común se lo denomina vértice del cono de paso, y es desde allí donde se genera la geometría de los flancos dentados.
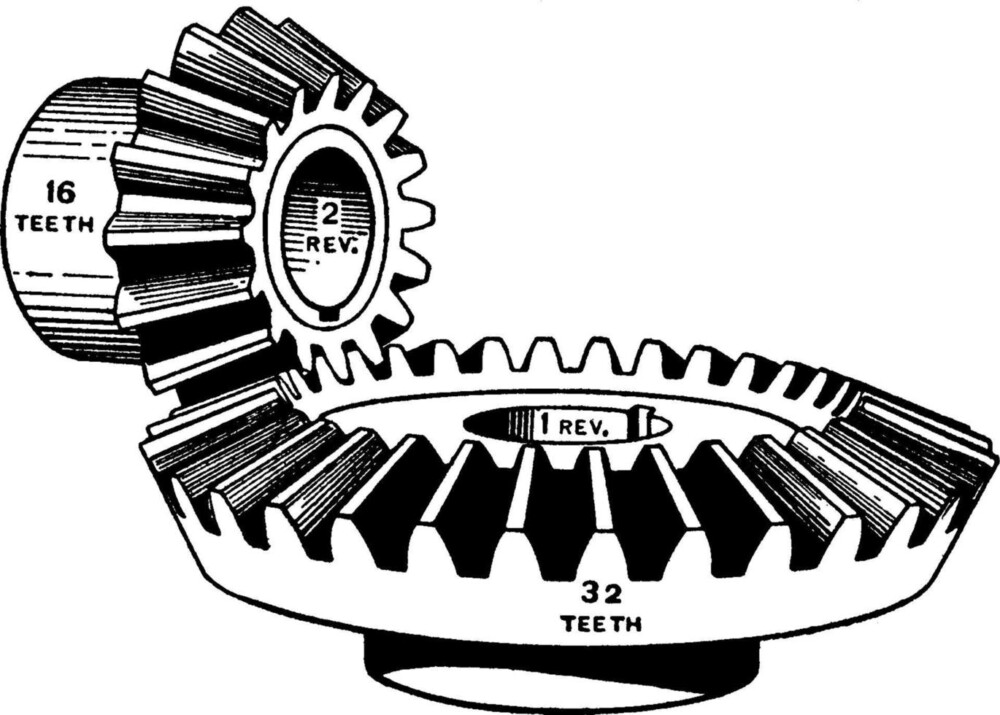
Cuando ambos engranajes tienen el mismo número de dientes y los ejes se cruzan a 90 grados, se obtienen engranajes cónicos de relación 1:1, conocidos como engranajes miter. Sin embargo, es habitual encontrar relaciones distintas, lo que permite modificar la velocidad y el torque de salida en función de las necesidades del sistema.
La acción de contacto entre los dientes ocurre progresivamente, lo que favorece una buena distribución de carga. No obstante, a diferencia de los engranajes helicoidales, el contacto entre dientes en los engranajes cónicos puede ser más puntual, lo que exige una mayor precisión en el montaje y en la fabricación para evitar concentraciones de esfuerzo que aceleren el desgaste.
Variantes de engranajes cónicos
Dentro del grupo de engranajes cónicos, existen diferentes configuraciones que responden a necesidades particulares. Uno de los más utilizados es el engranaje cónico espiral, donde los dientes presentan una curvatura helicoidal que mejora la progresividad del contacto y reduce el ruido. Este tipo es ampliamente usado en diferenciales automotrices debido a su suavidad y capacidad para transmitir altos torques.
Otra variante es el engranaje cónico hipoidal, cuyo diseño permite que los ejes no se crucen exactamente, sino que queden desfasados, generando un deslizamiento adicional entre los flancos. Esta configuración, común en los diferenciales traseros de vehículos con tracción trasera, permite reducir el tamaño del eje de transmisión y bajar el centro de gravedad del vehículo.
También existen engranajes cónicos rectos, donde los dientes son lineales y radiales al vértice del cono. Aunque su fabricación es más sencilla, generan mayor ruido y vibraciones que los espirales, por lo que su uso suele limitarse a aplicaciones de baja velocidad o a mecanismos donde el costo y la simplicidad son prioritarios.
Aplicación en la industria automotriz
En el ámbito automotor, los engranajes cónicos tienen un papel protagonista en los diferenciales, especialmente en aquellos que transmiten la potencia del eje cardán a las ruedas motrices. Aquí, el par cónico permite modificar el ángulo de transmisión, generalmente en 90 grados, y ajustar la relación final del eje para adecuar el torque a las necesidades del vehículo.
Su capacidad para soportar altas cargas y operar de forma eficiente bajo condiciones de trabajo exigentes los convierte en una solución ideal en vehículos de tracción trasera, todoterreno, vehículos pesados y también en ciertos sistemas de tracción integral. La incorporación de variantes hipoidales mejora aún más la capacidad de carga y la eficiencia en estos entornos.
Más allá del diferencial, también es posible encontrar engranajes cónicos en mecanismos auxiliares como sistemas de dirección, cajas de transferencia, y en maquinaria agrícola o industrial donde es necesario cambiar la orientación del eje de transmisión.
Consideraciones técnicas
El uso de engranajes cónicos exige tener en cuenta diversos factores en el diseño y montaje. Uno de los más críticos es la alineación precisa entre los ejes, ya que cualquier desviación puede generar una mala distribución de la carga entre los dientes, provocando desgaste prematuro o incluso fallos catastróficos.
Además, dado que estos engranajes pueden generar fuerzas radiales y axiales importantes, es necesario diseñar adecuadamente los rodamientos y soportes para absorber estas cargas y garantizar una operación estable y prolongada.
En aplicaciones donde el torque es elevado, como ocurre en vehículos 4×4 o camiones de carga, los engranajes cónicos deben fabricarse con materiales de alta resistencia, generalmente aceros aleados, y someterse a tratamientos térmicos como la cementación, nitruración o temple por inducción, para aumentar su dureza superficial sin perder tenacidad en el núcleo.
La lubricación también es un aspecto clave, ya que las condiciones de contacto pueden ser severas y generan calor. Se utilizan aceites específicos con aditivos de extrema presión (EP) que evitan el desgaste adhesivo y reducen el riesgo de micropitting.
Ventajas y limitaciones
Entre las ventajas de los engranajes cónicos se destaca su capacidad de transmitir potencia entre ejes no paralelos de forma eficiente y compacta. También ofrecen un gran rango de relaciones de transmisión y pueden adaptarse a diferentes geometrías del sistema mecánico.
Sin embargo, no todo es favorable. Comparados con otros engranajes como los planetarios o helicoidales, los cónicos son más exigentes en cuanto a precisión de montaje, mantenimiento y lubricación. Además, su fabricación requiere equipos especializados, lo que eleva su costo en comparación con otros tipos más sencillos.
Conclusión
Los engranajes cónicos son elementos esenciales en muchas transmisiones donde se necesita cambiar la dirección del movimiento rotativo y ajustar las condiciones de velocidad o torque. Su versatilidad, combinada con una alta capacidad de carga, los convierte en piezas clave dentro de sistemas de transmisión sofisticados, especialmente en la industria automotriz.
Su correcto diseño, montaje y mantenimiento garantiza un rendimiento confiable y duradero, lo cual explica su presencia sostenida en aplicaciones críticas desde hace más de un siglo. Para un ingeniero automotriz, comprender sus principios de funcionamiento, sus variantes y sus implicancias mecánicas es fundamental al momento de diseñar o reparar sistemas de transmisión complejos.