Los engranajes internos, también conocidos como engranajes de corona interna, son un tipo particular de engranaje cilíndrico en el que los dientes están tallados en la superficie interna de un anillo o rueda hueca. A diferencia de los engranajes externos, en los que los dientes se encuentran en la periferia exterior, en este caso los dientes están orientados hacia el centro. Este tipo de engranaje juega un papel esencial en muchos sistemas mecánicos que requieren una transmisión compacta y eficiente, especialmente en aplicaciones donde se necesita mantener la rotación de los ejes en la misma dirección.
Funcionamiento básico
El principio de funcionamiento de un engranaje interno es muy similar al de un engranaje externo, con la diferencia clave en la orientación y ubicación de los dientes. Cuando un piñón (un engranaje de menor tamaño con dientes externos) se acopla al engranaje interno, ambos giran en la misma dirección, lo que representa una ventaja en sistemas donde se desea evitar el cambio de sentido del giro.
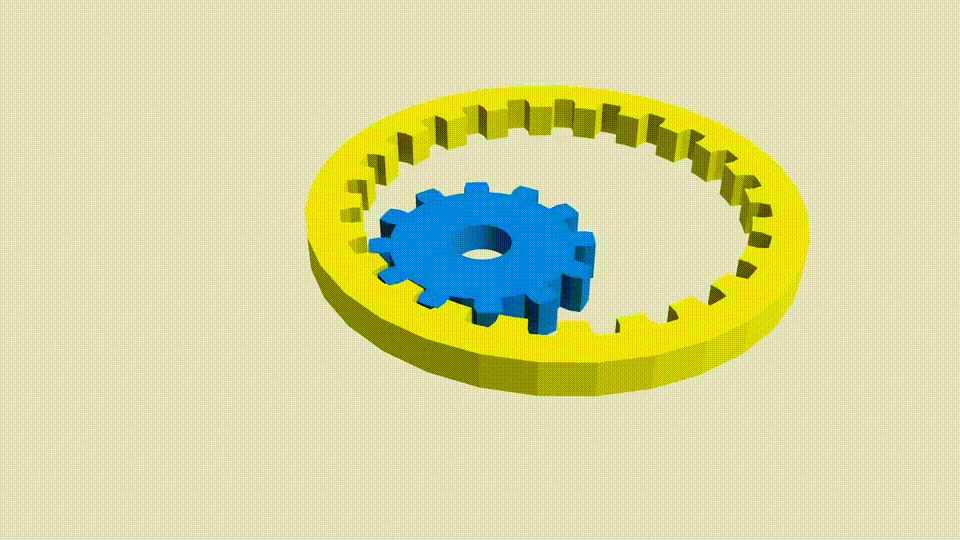
Este comportamiento se debe a que, al engranar un componente externo dentro de una corona interna, la interacción de los dientes no invierte la dirección del par de rotación, como sí ocurre en el caso de dos engranajes externos enfrentados. Esta característica es especialmente útil en mecanismos que buscan simplicidad y alineación directa del flujo de potencia.
Aplicaciones en la mecánica automotriz
En el campo automotriz, los engranajes internos son fundamentales en transmisiones planetarias, donde forman la corona o engranaje anular. En estos sistemas, los engranajes internos interactúan con los engranajes satélite, que a su vez giran alrededor de un engranaje solar central. Este tipo de disposición permite una gran variedad de combinaciones de entrada y salida, lo que se traduce en distintas relaciones de transmisión sin necesidad de aumentar el volumen del conjunto.
Dentro de las transmisiones automáticas tradicionales (AT), el engranaje interno es un componente crítico para permitir que el sistema funcione con múltiples relaciones de cambio, facilitando el cambio de marchas sin intervención del conductor. También está presente en transmisiones híbridas, diferenciales autoblocantes y mecanismos de transferencia de par en sistemas de tracción total.
Fuera del ámbito automotriz, los engranajes internos también se emplean en motores hidráulicos, turbinas, bombas de engranajes y sistemas robóticos donde se requiere una alta densidad de torque en un espacio reducido.
Ventajas del engranaje interno
Una de las principales ventajas de este tipo de engranaje es su compacidad estructural. Al permitir la inclusión del piñón en el interior del engranaje de mayor tamaño, se puede lograr una transmisión completa dentro de un volumen muy contenido. Esto resulta ideal para diseños donde el espacio es limitado, como ocurre frecuentemente en componentes automotrices modernos.
Otra característica relevante es la mayor cantidad de dientes en contacto simultáneo, lo que permite una mejor distribución del esfuerzo y una menor presión específica sobre cada diente. Esto contribuye a una mayor durabilidad del conjunto y una operación más silenciosa y suave, reduciendo vibraciones y ruidos indeseados.
Además, al no invertir la dirección del giro, los engranajes internos simplifican el diseño de ejes coaxiales paralelos, algo altamente valorado en aplicaciones donde el diseño debe ser simétrico o modular.
Consideraciones de diseño y fabricación
Diseñar y fabricar engranajes internos presenta desafíos particulares. A diferencia de los engranajes externos, que pueden ser mecanizados de manera relativamente sencilla mediante fresado o tallado convencional, los engranajes internos requieren métodos más especializados, como brochado, tallado con herramientas especiales o mecanizado por control numérico computarizado (CNC). Estas técnicas deben garantizar una alineación precisa y un perfil de diente adecuado para permitir un engranaje correcto con su contraparte externa.
Los materiales empleados deben ofrecer buena resistencia al desgaste y a la fatiga por contacto. En muchos casos se utilizan aceros cementados, nitrurados o endurecidos por inducción, y frecuentemente se recurre a tratamientos térmicos que mejoran la dureza superficial sin comprometer la tenacidad del núcleo.
El juego entre los dientes del piñón y el engranaje interno también debe ajustarse cuidadosamente para evitar un funcionamiento áspero o, por el contrario, un engranaje flojo que derive en ruidos o fallos prematuros. Estos aspectos son especialmente críticos cuando el engranaje interno forma parte de un conjunto planetario, ya que deben engranar simultáneamente con varios piñones.
Comparación con otros tipos de engranajes
Aunque los engranajes internos se clasifican como engranajes cilíndricos, su comportamiento se diferencia de los engranajes rectos y helicoidales en cuanto a configuración y dirección del flujo de potencia. Su relación de transmisión depende del número de dientes tanto del piñón como de la corona, y su comportamiento puede ser tanto reductor como multiplicador, según cuál de los dos actúe como entrada.
En comparación con un sistema de engranajes externos equivalente, el tren que incluye un engranaje interno puede ofrecer mayor eficiencia en términos de espacio, aunque puede ser más complejo de fabricar. Además, su disposición permite configuraciones coaxiales que no son posibles con engranajes externos, una ventaja importante en transmisiones modernas donde la alineación entre motor y salida debe mantenerse centrada.
Conclusión
El engranaje interno es una solución altamente eficiente y compacta para la transmisión de potencia en sistemas mecánicos exigentes, como los que se encuentran en la industria automotriz. Su capacidad para mantener la dirección del giro, su disposición concéntrica y su excelente aprovechamiento del espacio lo convierten en un componente clave en transmisiones automáticas, trenes planetarios y mecanismos de reducción de alta precisión.
Comprender su funcionamiento y sus particularidades constructivas no solo permite un mejor diseño e integración en vehículos, sino que también facilita tareas de diagnóstico y reparación en sistemas complejos. Su estudio continúa siendo relevante tanto para ingenieros como para técnicos especializados en la evolución de la movilidad y la eficiencia mecánica.